0 引 言
如何保证制造的生产效率是当前国内企业把握并获取竞争优势的必要手段,有效的制造绩效评价(Manufacturing Performance Measurement)系统对生产运作管理的效率改善起着极其重要的作用。20世纪90年代起,Fry,Bondt,Fullerton,Kuwaiti和Shaeffer等人高度评价了制造绩效评价在持续改善、业务流程重构和企业资源计划等实施过程中所带来的裨益,认为制造绩效评价有助于企业决策,有助于改善车间控制,帮助企业员工和管理人员了解业务流程,明确责任和目标,帮助企业发现现有系统的不足,挖掘生产系统的潜力,以及帮助企业改善运作或对信息化改造项目实施评价等。
本文在当前制造绩效评估研究基础上,提出了制造绩效测量系统的概念设计及基于流程的制造绩效评价系统模型,强调了评价指标间的交互关系,实现了对制造业企业面向效率改善的有效制造绩效评估。
1 制造绩效评价系统框架分析
1992年,Kaplan和Norton首先提出了平衡记分卡(balanced scorecard)的绩效评价系统框架,从财务、内部业务流程、顾客以及学习与成长4个方面对企业的绩效进行综合评价(如图1)。在帮助企业将抽象的企业战略自上而下地具体化为可执行的运作目标的同时,将非财务性指标提到了企业战略的高度,以克服以往单一的财务性评价所带来的缺陷。但是在基本绩效指标方面,平衡记分卡没有考虑企业竞争对手的影响,特别是对外部环境施加在企业绩效的影响考虑不足。此外,也没有区分各绩效体指标在时间尺度上的差异。

图1 平衡记分卡
Bititci提出从控制视图、数据视图和过程视图3个方面建立集成化的绩效评价系统,每个视图都配备了相应的分析工具(如图2),这样既明确了绩效评价系统的功能,又给出了系统设计的大致过程。
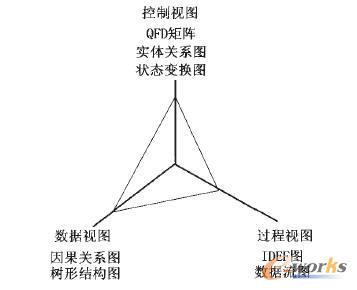
图2 Bititci提出的绩效评价系统视图模型
White以制造绩效指标之间的相互影响为基础,绘制了最初的、定性的制造绩效指标关系网络;Suwignjo等人描述了各绩效指标之间的定量关系,将交互关系分为直接影响、间接影响和自我影响3类,绩效指标对目标的最终影响通过综合这3种影响来计算分析(如图3)。
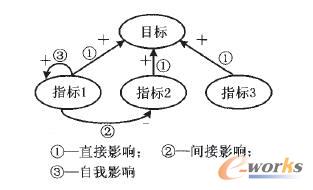
图3 绩效指标间的影响分析
综合以上概念模型、关系分析和指标分类等一系列思想,Bititci提出了“集成化绩效评价”和“动态绩效评价”的概念,考虑了对不同绩效指标的集成,以及绩效评价系统对外部环境变化的适应。结合层次分析法(Analytic Hierarchy Process,AHP),制造绩效评价可应用在对不同制造策略的评价中。
现场改善是现场生产管理最为有效的方法之一,如何将现场改善纳入制造绩效评价系统是面向制造业现场管理的研究热点。Daniels建立了主动绩效评价系统(proactive performance measurement system)的概念。Ghalayini等人提出的“集成化动态绩效评价系统”(integrated dynamic performance measurement system)更加强调了绩效评价与持续改善之间的关系。如图4所示,该系统模型将企业管理、车间管理和过程改进小组对绩效评价的不同要求联系起来,这3个方面的绩效评价各有侧重、互为补充。
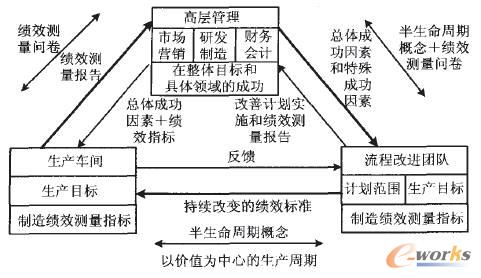
图4 集成化动态绩效评价系统模型
绩效评价系统的有效性还表现在设计过程方面,Flapper等人首先提出绩效评价系统设计应分为定义绩效指标、分析绩效指标之间的联系和设立绩效指标目标值3个主要步骤。Neely等人将绩效评价系统的设计分成了更详细的12个步骤。针对已经设立了绩效评价系统的企业,绩效系统设计按照如图5所示的步骤进行。Neely认为,绩效评价系统的设计是以对企业流程的分析为基础的。可以认为这种基于流程的制造绩效评价与工作流管理(workflow management)的思想是一致的,已有学者尝试将两者的思想结合起来提出新的制造绩效评价工具。
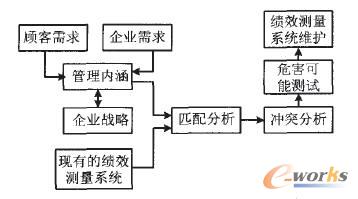
图5 Neely提出的绩效评价系统设计流程2 制造绩效指标设计
2.1 绩效指标的分类和设立原则
绩效评价可从企业内部设置(internalco nfiguration)和外部表现(external configuration)两方面进行,并产生相应的绩效指标类别。Neely等人也提出绩效评价应区别为对系统内部流程效率(efficiency)的评价和对制造系统外部效果(effectiveness)的评价。Flapper等人则主张从财务性指标与非财务性指标、全局指标与局部指标、内部指标和外部指标、组织层次以及应用范围等多个角度对绩效指标进行分类。Neely等人提出了质量、时间、成本和柔性4个大的类别,得出了22条绩效指标设立的原则,这些原则为绩效评价系统筛选绩效指标提供了依据;White等人则将制造系统的绩效指标分为质量、成本、柔性、交付可靠性和速度5个方面。但是,某个具体的绩效指标只能部分满足以上要求,只有建立完整的指标体系才能提供正确的制造绩效评价依据。
2.2 面向财务的指标体系
财务性指标是较早应用于绩效评价的指标类型,1917年杜邦公司的创始人Pierre S.Du Pont为衡量其公司内部不同部门的绩效而设立了投资收益率(Return On Investment,ROI),其计算经常采用如下公式:

式中,对于制造系统,收入即为制造系统的产出品所对应的价值;成本为生产活动的支出,传统的会计系统往往将其划分为劳力成本、原料成本和一般性开支;而资本的定义比较复杂,可以从不同的方面来考虑,并且涉及资产计价的问题。Hopp将制造系统的资本一项计为可控资本,如库存等。
生产率(productivity)是另外一种与财务性指标密切相关的绩效指标,表示制造系统的有效输出与消耗资源的比例。Sink系统地提出了3种生产率评价方法,即单指标生产率评价法(Normative Productivity Measurement Methodology,NPMM)、多指标生产率评价法(Multi-Factor Productivity Measurement Model,MFPMM)和多准则生产率/绩效评价方法(Multi-Criteria Performance/Product Measurement Technique,MCP/PMT)。值得注意的是,Sink等人提出的生产率管理(productivity management)的概念,超出了单纯财务性质的生产率概念,延伸到了绩效指标方面(如质量、时间等)。
传统的财务性指标和生产成本计量方法具有较大的局限性,主要包括:①传统的财务性指标鼓励短期性决策;②传统的会计无法正确地将一般性开支进行划分,因而不能对产品的成本作出正确的结论;③传统的会计系统不能支持学习和生产系统的改进;④财务性指标不能提供实时信息。
针对以上缺点,Cooper于20世纪80年代中期提出了作业成本法(Activity Based Costing,ABC),将作业分析和成本计量结合起来,但是仍然存在一些不足。ABC方法在某些情况下难以做到生产成本对某一生产活动的归属;其次,ABC方法往往不将产品生产过程中出现的机会成本纳入考虑范围,而又有可能将某些不应纳入计算范围的沉没成本计入产品成本中。其他一些生产成本计量方法,如Galloway和Waldron以及Dugdale和Jones等人将约束理论应用于管理会计系统的设计中,提出了产销率计算(throughput accounting),但该方法只关注于过去的市场完成情况进行统计和计量评价。
2.3 面向质量的指标体系
质量管理大师Juran对质量的定义是“可用性”(fitness for use),然而这种宽泛的定义并不能适合生产管理中实际操作的要求。为满足制造绩效评价中定量化的要求,需要对质量给出更细致、更具体的定义。Garvin提出应该从性能、特色、可靠性、一致性、耐久性、可维护性、美观程度和可被察觉的质量等8个方面衡量。
随后,质量的经济效益被重视起来。Crosby认为企业由于采用了质量提高措施而得到的收益将超出企业在这方面的投入,因此提出“质量是免费的”。“质量成本”(quality cost)的提出反映了质量的这种特性。Feigenbaum提出质量成本分为控制成本和控制失效成本2个大类4个方面,即预防成本、评估成本、内部故障成本和外部故障成本;Dale等人提出,质量成本还可以按照产生的原因进行分类,分为与供应商相关的质量成本、与本企业相关的质量成本和与客户相关的质量成本。
但是,用成本的表现形式反映生产系统的质量绩效也存在一定的问题。如Dale等人提出质量成本中质量和成本的关系可能会造成企业管理者对质量的错误理解,使其认为存在一种类似于库存管理中EOQ模型的最佳质量水平,这对于企业的长期发展可能不利。此外,质量成本通常与企业运作引起的其他成本揉合在一起,所以很难对其精确划分。意大利学者Toni认为质量成本只是衡量生产系统质量绩效的一个方面,他对质量进行了新的定义,从企业、顾客和质量成本3个方面对质量绩效进行衡量。而对于制造系统,企业所提供的质量是研究的重点,需要进行更细的划分。
全面质量管理(Total Quality Management,TQM)概念的出现使质量指标有了丰富的内涵。表1是1991年度和2003年度美国国家马科姆·巴德里奇质量奖质量衡量指标的对比。
表1 马科姆·巴德里奇质量奖评价原则
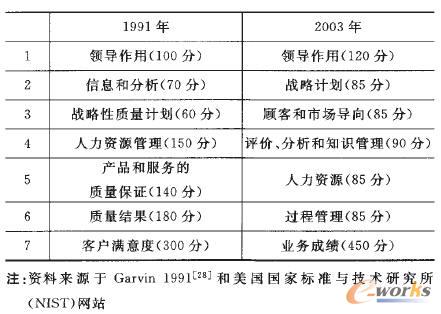
可见,质量的定义有着扩大的趋势,对它的衡量越来越趋向于涵盖企业管理的各个方面,这种趋势也使得质量评价越来越复杂。
2.4 面向时间的指标体系
时间指标是制造系统评价的重要性指标。中岛清一和今井正明都把消除制造系统中的浪费(muda)作为日本企业管理思想的重要组成。很多浪费是以时间来衡量的,如设备故障造成的时间损失、设备准备和调整造成的时间损失、待工和设备停顿、加工速度下降、加工流程错误造成的时间损失和产出率下降造成的时间损失等。
全员生产维护(Total Productive Maintenance,TPM)的概念从定义的时间损失入手,将消除时间损失作提高生产管理水平的重要手段。
Stalk提出了基于时间竞争(time-based competition)的概念,强调了时间指标对于企业绩效评价的重要性。Toni等人对各种时间指标进行了分类:
(1)内部时间指标指不能被企业外部顾客直接察觉的时间指标,如上市时间、生产提前期等;
(2)外部时间指标指能够被顾客直接感受到的时间指标,如新产品投放间隔、交货速度等。
这种时间指标的分类与上述绩效指标设立原则中的内部和外部是一致的。对时间指标的定义不同,企业采取的竞争策略也不同。如Toni将企业对于时间指标的竞争策略分为基于产品(productbased competition)和基于过程(process-based competition)两种,也指出了内、外两种时间指标之间存在的依存关系(如交付速度和可靠性)都与生产系统内部的时间绩效紧密相连。Hum将针对时间绩效的管理模型分为确定最佳/最短时间、提前期与库存的关系以及缩短生产准备时间和生产周期等3个类别。
2.5 面向柔性的指标体系
生产系统柔性的定义和度量在近20年以来引起了众多研究者的兴趣,并陆续提出面向制造系统柔性的评价指标。Slack提出柔性指标包括产品柔性(product flexibility)、混流生产柔性(mix flexibility)、产量柔性(volume flxibility)和交货柔性(deliveryf lexibility)4个方面。而Gerwin提出的柔性定义由混流生产柔性、改动柔性(modification flexibility)、路径柔性(rerouting flexibility)、产量柔性和物流柔性5方面组成。但是面对如此众多的柔性指标,如何找出其中的共性和差别,如何比较精确地量化,一直没有很好的方法。
Shewchuk提出从6个尺度上对柔性指标进行定义,即制造任务的明确程度、制造系统自身、环境因素、柔性尺度、柔性评价方式和时间尺度。其中,在柔性类别方面,根据柔性指标的内涵分为5大类:运作柔性(operational flexibility),范围柔性(range flexibility),反应柔性(response flexibility),动作柔性(action flexibility)和状态柔性(state flexibility)。该方法避免定义大量繁杂的柔性指标,规范和简化了制造系统柔性的度量。Toni提出从柔性的定义、对柔性需求的起源、柔性的尺度、柔性的评价、柔性的选择以及柔性的实现等6个方面对柔性指标进行划分,但在柔性的尺度方面与Shewchuk不尽相同。针对生产系统中人的因素,刘曙光等人提出从结构柔性、人员柔性和组织间关系柔性等衡量企业组织的柔性,但相应的柔性指标和度量仍需要进一步的研究。
2.6 面向综合的制造绩效指标体系
综合设备效率(Overall Equipment Efficiency,OEE)是综合型绩效指标的典型,由中岛清一在TPM的概念中提出,其基本公式为:

OEE综合了生产设备维护、效率和质量等多方面因素,是一种综合性评价工具,在工业界获得了广泛的应用。OEE已有应用局限性,如Ljungberg提出,OEE对时间浪费的计量集中在计划外的停顿时间上,而对计划内的时间损失关注不够,不利于制造系统的改进。OEE也不能反映制造系统绩效与企业整体战略之间的关联,同时,OEE只评价某个生产单元或流程的绩效,缺乏反映整个供应链绩效的能力。
Ron提出了与OEE类似的转换因子(Transformation Factor,TF)的概念,其定义为时间利用率和成品率的乘积):

从该定义可以看出,转换因子综合考虑了制造系统在时间利用和质量控制方面的绩效。3 绩效评价的系统方法
3.1 定性化评价系统方法
对制造企业绩效评价的定性化评价系统方法应首推标杆管理(benchmarking)。标杆管理也称定点超越,是在确定了绩效指标后,将被考察企业的情况与行业领先者的情况加以比较,从而得出各绩效指标的量值。Garvin在其对质量管理的论述中曾比较了美、日之间汽车工业的差距,该论述被认为是标杆管理思想的最早应用。标杆管理可以分为内部标杆管理、竞争性标杆管理、功能标杆管理和一般性标杆管理4种形式,但是其在制造绩效评价中的作用也存在不足。标杆管理的比较对象往往与其使用者存在竞争关系,因此用于标杆管理的数据采集通常十分困难。另外,即使是同行业、同职能之间的生产部门也往往面临不同的具体情况,标杆管理中选取的参照和使用者可能不存在可比性。相对更可行的标杆管理应该是“内部标杆管理”,即将企业的实际绩效与理论绩效相比较。目前标杆管理在制造业中的应用相对其在服务业中的应用还比较少。
Goodson提出的快速工厂阅读法(Rapid Plant Assessment,RPA)是一种与标杆管理有着相似思路的绩效评价方法,差别主要是它以专家经验为参照,将研究范围集中在制造系统。RPA将生产系统的绩效分为11个大的方面、20个调查问题和涉及成本管理的一系列表格,通过对制造车间现场的观察,结合评价团队的工作,快速得出对该生产系统的评价。
3.2 定最化评价系统方法
定量化评价系统方法主要包括AHP、多元统计分析和数据包络分析(Data Envelopment Analysis,DEA)。美国著名运筹学家Saaty于20世纪70年代提出AHP,其本质是一种决策思维模式。Saaty也将其称为一个评价的过程,即定量地标示出被选方案在一定准则下的优劣程度。AHP将复杂的问题分解为多个组成因素,按照组成因素之间的支配关系形成有序的递阶层次结构,通过两两比较的方式确定层次中各因素的相对重要性,然后确定被选方案的优劣。
AHP在绩效评价中通常被应用于确定各绩效指标的权重,即确定各绩效指标的重要性,但也具有一些不足,如逆序现象(Rank Reversal)。同时,AHP建立在严格的递阶层次结构的基础上,为了对层次元素间存在的相互作用情况进行分析,Saaty又进一步提出了更通用化的网络分析法(Analytic Network Process,ANP ),以超矩阵(super matrix)为主要工具,反映各元素之间的相互影响或关联。ANP在绩效评价中可以得到很好的应用,以ANP代替AHP建立绩效评价系统,可以更精确地反映绩效指标之间的关系。
多元统计分析是绩效评价中常用的分析手段,可以分为依存性(dependency)分析和相关性(interdependency)分析两类。前者旨在验证假设的指标依存性关系是否成立,相应的方法包括回归分析、差别分析等;后者用于分析不同指标之间的相互关系,区分不同的指标类别以及主要和次要因素等,相应的分析方法有因子分析、主成分分析、聚类分析和多维标度等。
著名运筹学家Charnes和Cooper等人在相对效率评价的基础上提出DEA的系统分析法。DEA方法的基本研究对象是决策单元(Decision Making Units,DMU),其基本思路是通过对一组DMU的输入和输出进行线性组合,得到有效生产活动的外包络面来比较各个DMU的相对有效性。1978年,Charnes,Cooper和Rhodes提出了第一个DEA模型——C2R模型,此后,C2GS2模型、C2WH模型、加性DEA模型、C-D型DEA模型以及含偏好信息的DEA模型等被相继提出并应用于实践。DEA方法所比较的对象具有3个特征:①相同的目标和任务;②相同的外部环境;③相同的输入和输出指标。这些特点使得DEA方法的应用范围具有一定的局限性。同时,DEA方法只能对分析得出的无效的DMU提供决策信息,而对于其他有效的DMU提供的信息则相对较少。
4 现有制造绩效评价系统的不足
除了前文中论述过的个别绩效评价系统的缺陷之外,本文从系统性上进行对现有制造绩效评价体系的不足进行了总结。
首先,目前的制造绩效评价系统对各绩效指标之间交互关系的处理还不够明确。一种观点认为,绩效指标之间的冲突是不可避免的,管理者必须在不同的指标之间做出折中(trade-off);而对立的观点认为,制造系统改善带来的往往是多个绩效方面的提高,因此所谓的折中是不存在的。Mapes的调查支持了后一种观点,但该调查是基于对多个企业的比较。如何在绩效评价系统中同时反映各绩效指标之间的相互促进和交替关系,目前还没有完善的解决方法。
其次,在制造绩效评价中,虽然绩效指标的量化通常采用客观的方法,但对指标权重的判定及指标之间关系的分析却主要依靠主观判断。因此,绩效评价结果对评价者的经验和思维模式依赖性很大,这些都限制了绩效评价系统的广泛应用。制造系统相对于服务业来说,因更多地受物理条件的限制而具有更高的可预见性。因此,如何根据制造系统自身的特点发展出更具客观性的绩效评价系统,仍然值得深入研究。
再则,现有的绩效评价系统不能区分控制指标(control measure)和改进指标(improvement measure)。虽然已经有绩效评价系统强调了改善小组在制造绩效评价系统中的作用,但是其作用只是对绩效指标的更新,并没有从本质上反映运作改善对绩效指标的要求。
最后,在目前的绩效评价系统中,确定性的因果关系是基本的逻辑框架,如平衡记分卡中所蕴含的“创新→内部流程改进→顾客满意度提高→财务表现提高”因果关系链。对于复杂的生产系统,类似于物理学中量子力学的不确定性理论应该应用到绩效评价中来。制造系统中的不确定性(uncertainty)和多样性(variability)对其绩效有着显著的影响,如何度量和处理这些对应关系都是重要的问题。
5 基于流程的制造绩效评价体系
本文提出了一种基于流程分析的绩效测量系统设计流程。基于流程分析的绩效测量与评价是综合考虑企业管理中的纵向过程(由顶向下的战略分解)和考虑生产运作管理的横向过程(对流程的建模和分析),如图6所示。
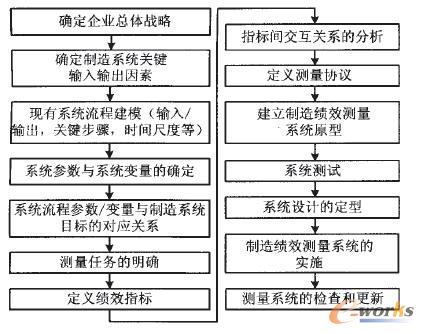
图6 基于流程分析的制造绩效测量系统设计
在此制造绩效测量系统设计流程的基础上,设计了制造绩效测量的系统模型,如图7所示。其中,系统分为绩效指标群、独立指标及指标间相互作用的网络层、对绩效指标的测量和报告进行规范的协议层3个层次。
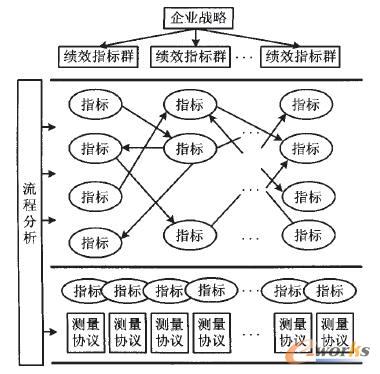
图7 制造绩效测量系统模型
指标群具有外部性,反映出外部环境对制造系统输出的预期要求。指标群之间还存在交替关系,使得可以利用此模型结合AHP及ANP对各个指标群的重要性进行量化和排序;而网络层中,利用实际生产数据、生产管理人员的专家知识以及对制造系统的仿真实验进行量化,而后利用ANP中的超矩阵,将所有因素间作用给予建模,并计算极限影响矩阵;协议层包括测量协议(绩效指标名称、绩效指标的计算公式、绩效指标测量方法、绩效指标测量频率和测量人员)、报告协议(指标名称和测量时间、指标报告对象、指标与企业或部门战略的关系、指标对应的相关职能和部门、指标的目标值和实际值、指标阶段变化趋势)和反应协议(指标变化原因、指标变化的应对措施建议、应对措施的实施部门和人员建议)。限于篇幅,具体案例的应用将在后续文章进行介绍。
6 结束语
制造绩效评价系统越来越趋向于集成化和动态化,涉及到生产系统的各个方面。在制造绩效指标方面,针对制造系统的特点,需要建立客观的、可快速获取的并能反映生产过程特点的制造绩效指标;对于制造系统中的不确定性,应设定相应的的绩效指标;对于生产控制和生产改善的不同需要,应加强制造绩效指标的针对性。绩效评价系统的作用不仅是利用当前或者过去的信息判断已经发生的事件,还应该以得到的信息预见将来可能发生的事件,及早采取相应的措施。基于流程分析的制造绩效评价模型可以实现面向生产系统的不确定性和变化性的综合评价,并实现基于物流及供应链绩效的制造绩效指标设计。